High Torque BL-Motors
ATEC ROBOTICS LIQUID COOLED BRUSHLESS MOTORS
ATEC Robotics designed and manufactures high performance liquid cooled brushless motors up to 1700Nm peak torque. They are used for large systems ìdirect drive. namely radar, pointing systems, telescopes, radiotelescopes. Driven with ATEC Robotics zero backlash control system ATEC Torque Motors represent the higher quality solution. In case of professional astronomical applications each section of the motor is maintained within +/-0.5 degs in respect to ambient and mechanical interface temperature.

Description
The BRT series brushless servomotors has been designed for direct coupling to shaft load. The possibility to achieve very high torque at low rotational speed ensures very high accuracy up to 0.1%.
The BRT series includes three modular sizes amd some intermediate models; continuous duty torque ranges from 26 up to 460 Nm and peak torque from 83 up to 1750 Nm with the no cooled version. The cooled versions allow an increase of 50% of the duty torque ranges.
The torque/mass ratio achieves 2.3Nm/kg if referred to the continuous duty and 8.6Nm/kg if referred to peak torque.
Windings of the BRT servomotors have been designed for 180V or 325V (in the table below the 325V version is the V type).
The BRT series meet norm for industrial environment according to 89/336/CEE (EMC).
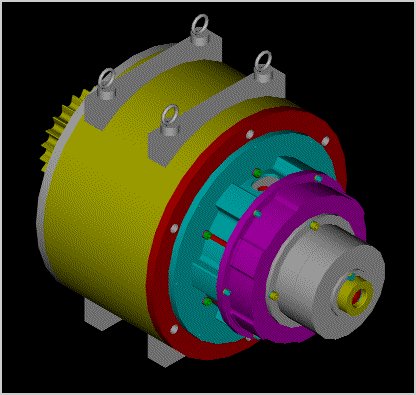
Some system composed by 8 motors has been mounted on the Galileo Altazimuthal Italian Telescope (Canary Islands) and on the VST (Very Large Telescope Survey Telescope), providing the state-of-the-art in the field.
Standard Models
- flux concentration magnetic circuit with Ferrite magnets
- 3-phase wye connected winding
- IP54 protection, according to EN600034-5 (1988)
- servomotor number of poles 12
- resolver number of poles 6
- class H insulation
- embedding with a special resin to optimize the thermal dissipation
- ambient temperature -20°C - +55°C
- storage temperature -25°C-+70°C
- winding thermal protection using PTC (threshold at 130°C)
- ball bearings with encreased radial play (C3), shielded, lubricated for life, equipped with temperature grease (170°C)
- cylindrical shaft for direct coupling mechanical interface with threaded hole according to DIN332 (1983) to provide load matching with no axial load on the bearings
The motor interface and the pinion shaft interface can be prepared on the base of the custom requirements.
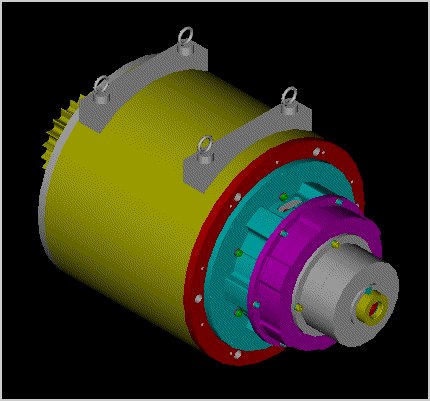
- connectors (PT or 97B type) for quick connection of Power, Resolver and thermal protection (separate). Plug connector included.
- connectors (PT or 97B or DB) for quick connection of tachometer and brake (separate)
- dynamic balancing accuracy Q=2.5 according to ISO1940-1
- black or aluminum finished
Cooled Versions
- cooling chamber around stator
- cooling flow required: depending on the power absorbed - up to 10 lt/min or more
- cooling fluid inlet temperature min: -20°C
- rated power improvement: up to 60%
- up to 3 (or more) PT100 or XX592 (absolute) sensors included (at motor flange, at brake level, on external body, at inlet fluid flange, at outlet fluid flange)
- M20 threaded holes (20 mm deep) for inlet/outlet piping
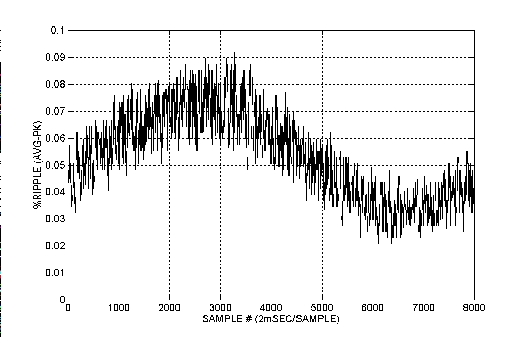
More Technical Info
The motors can work in the minimal configuration without tacho and brake. In combination with an ATEC digital drive is possible to receive simulated position informationa and or speed, and can be driven in speed and torque. This possibility is essential for that system where a precision of about 30 arcsec at the motor shaft is acceptable.
The motors can be furnished with and without pinions. In case of no pinion a cylindrical shaft is available for direct coupling with threaded holes according to DIN332 (1983) to provide load matching with no axial load on the bearings. The motor pinion can be customized or removed. Some pinion design are already available. The motor interface (motor shaft) can be easily adapted to the customer applications.
The motors can be driven in pairs (2 or more couple of motors, see picture below) in an adaptive preload configuration, using the ATEC adaptive preload Magellano system. This module allows to drive the motors removing completely the backlash and by providing the best amount of torque (adaprive) related to the torque request from the mechanical system. The torque level is optimized in order to minimize the system consumption and the thermal losses. The system allows to maintain always the minimal ripple torque at the motor shaft (the ripple is proportional to the actual torque request).
The BRT series are modular, namely the possibility to remove some components such as the high performance tachometer, the brake or the encoder.
The motors are equipped with an high performance low ripple tachometer, a brake and can support high resolution axis encoder, linked to the motor axis by means of a special ATEC patented solution (coaxial free shaft from the encoder to the pinion free face).
The motor can be equipped with ATEC digital drive allowing high level motion performance. Each drive is capable to support up to 3 motors and can be driven in speed or torque.
The motors can be furnished in pairs with a dedicated ATEC controller for adaptive preload configurations, such as large astronomical telescopes, antennas, large plants.
Motor Technical Characteristics
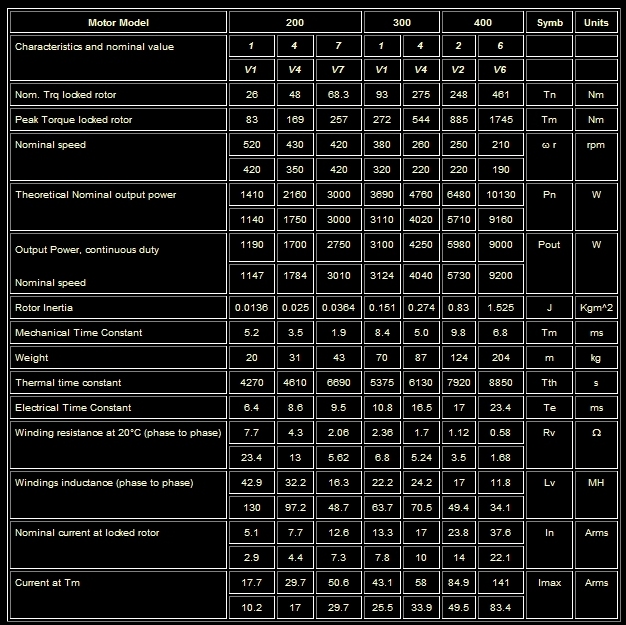
Tachometer technical characteristics
Thacometer is not indispensable depending on the control system architecture. For high level applications speed reference signal is obtained by means high quality tachometers namely the model QRG-7201 by Inland, a leading in tacho manufacturring. The tacho ripple is less than the 0.1% of the nominal output voltage (data sheet value). This is achieved through a fine adjustment of the magnetic field by means of an accurate positioning of any single field magnet during tacho integration and measurement test. In the picture below a sample of one reference tachometer output voltage ripple is shown. The use of low ripple tachometers provides good accuracy in velocity feedback even at near-zero speed.
It is also possible to integrate Hollow-Shaft encoders for speed and position loops. The interface can be prepared on the base of customer design.
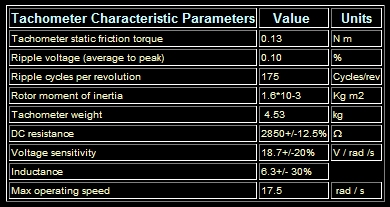